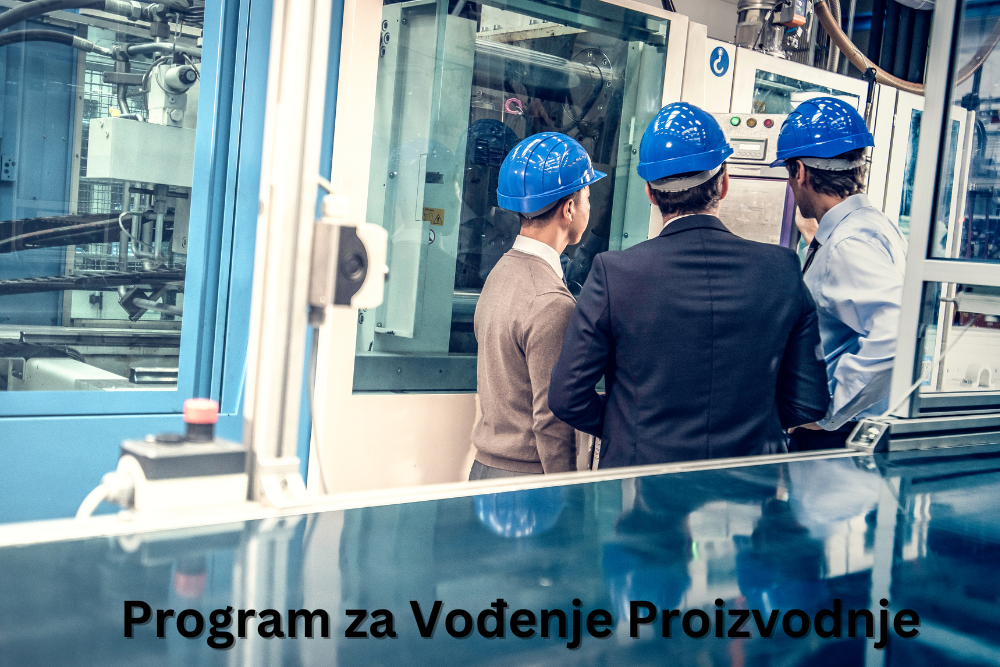
U današnjem brzom proizvodnom okruženju, efikasnost i preciznost su kritične. Programi za proizvodnju postali su suštinski alati za proizvođače, pomažući da se pojednostave procesi, smanje troškovi i maksimizira produktivnost. Ali šta tačno nudi program upravljanja proizvodnjom i kako može da transformiše operacije?
Efikasno upravljanje skladištem je okosnica dobro vođenog lanca snabdevanja. Ipak, mnoga preduzeća postaju žrtve uobičajenih grešaka koje mogu ometati poslovanje, povećati troškove i dovesti do nezadovoljstva kupaca. Identifikovanje i rešavanje ovih grešaka može povećati produktivnost, smanjiti troškove i poboljšati zadovoljstvo kupaca. Hajde da zaronimo u pet najvećih grešaka u upravljanju skladištem i kako ih izbeći.
Softver za praćenje zaliha , takođe poznat kao program za upravljanje zalihama , je specijalizovani alat ili aplikacija dizajnirana da pomogne preduzećima da efikasno prate, upravljaju i optimizuju svoje nivoe zaliha i povezane procese. To je tehnološko rešenje koje pomaže u nadgledanju čitavog životnog ciklusa zaliha, od nabavke i skladištenja do prodaje i ispunjenja.
MRP je skraćenica za planiranje materijalnih potreba, i to je ključni koncept u proizvodnji i upravljanju proizvodnjom. To je metod koji se koristi za planiranje i upravljanje zalihama, obezbeđujući da su materijali dostupni za proizvodnju uz minimiziranje troškova nošenja.
Cilj MRP-a je da optimizuje nivoe zaliha, minimizira troškove transporta, spreči nestašice i obezbedi da proizvodnja zadovoljava potražnju bez preteranog viška. MRP sistemi su često integrisani sa drugim sistemima za planiranje resursa preduzeća (ERP) kako bi efikasno upravljali različitim aspektima poslovanja kompanije.
Od 2019. godine, preduzeća širom sveta doživela su ogromne poremećaje u lancima snabdevanja u nizu industrija, stvarajući nestabilnost i neizvesnost.Nekoliko faktora je doprinelo tome:
Automatizovani sistem upravljanja zalihama je softverski vođeno rešenje koje koristi tehnologiju za praćenje, kontrolu i optimizaciju zaliha preduzeća na efikasniji i tačniji način u poređenju sa ručnim metodama. Ovaj sistem pojednostavljuje ceo proces upravljanja zalihama, od praćenja nivoa zaliha do popunjavanja artikala i generisanja izveštaja.
E-trgovina, skraćenica za elektronsku trgovinu, odnosi se na kupovinu i prodaju roba i usluga preko interneta. Transformisala je način na koji preduzeća funkcionišu i način na koji potrošači kupuju, nudeći digitalnu platformu za transakcije, komunikaciju i interakciju između kupaca i prodavaca. E-trgovina obuhvata širok spektar aktivnosti, poslovnih modela i tehnologija koje olakšavaju onlajn trgovinu.
Planiranje proizvodnje se odnosi na proces kreiranja i organizovanja detaljnog plana za izvođenje proizvodnih aktivnosti u proizvodnom okruženju. To uključuje određivanje redosleda i vremena zadataka, dodelu resursa i koordinaciju različitih proizvodnih aktivnosti kako bi se obezbedio nesmetan i efikasan tok operacija.
Cilj planiranja proizvodnje je optimizacija korišćenja raspoloživih resursa, minimiziranje zastoja, smanjenje troškova i ispunjavanje proizvodnih ciljeva ili zahteva kupaca u određenim vremenskim okvirima. To uključuje razmatranje faktora kao što su proizvodni kapacitet, dostupnost resursa, prioriteti narudžbi i ograničenja kako bi se napravio izvodljiv i efikasan raspored.
Serijska proizvodnja je proizvodni metod gde se istovremeno proizvodi ograničena količina određenog proizvoda. To uključuje podelu proizvodnog procesa na različite faze i proizvodnju određenog broja jedinica u svakoj fazi pre nego što se pređe na sledeću seriju. Svaka serija obično prolazi kroz ceo proizvodni proces, od pripreme materijala do montaže, testiranja i pakovanja.
Izgradnja efikasnog sistema upravljanja skladištem zahteva pažljivo planiranje, pažnju posvećenu detaljima i primenu najboljih praksi. Evo nekoliko koraka koji će vam pomoći da izgradite efikasan sistem upravljanja skladištem:
Softver za upravljanje proizvodnjom je alat koji može pomoći preduzećima da steknu uvid u svoje proizvodne procese pružanjem podataka i analitike u realnom vremenu. Korišćenjem ovog softvera, preduzeća mogu da prate i prate svoje proizvodne tokove, identifikuju uska grla i optimizuju svoje poslovanje kako bi poboljšali efikasnost i smanjili troškove.
Pojednostavljeni softver za fakturisanje pomaže vlasnicima malih i srednjih preduzeća da prate koju robu i usluge pružaju kupcima i koliko ti klijenti duguju. Najbolji softver za fakturisanje omogućava preduzećima da upravljaju procesom naplate od početka do kraja, od kreiranja procena za nove projekte do praćenja odrađenih sati do prikupljanja uplata. Naš najbolji softver za fakturisanje nudi ove funkcije i više da vam pomogne da ostanete organizovani. Vlasnici malih preduzeća provode dosta vremena upravljajući delikatnim odnosima sa kupcima. Iako je važno imati prijateljsko lice, važno je i povući granice, posebno kada su u pitanju uslovi plaćanja.
Ukoliko imate proizvodnju potreban vam je softver koji je pouzdan i zadovoljava sve vaše proizvodne potrebe. Bez obzira na veličinu vašeg poslovanja ili vrstu industrije, softver za vođenje proizvodnje podiže vaše poslovanje na viši nivo.